- Farm & Garden
- Pumps & Motors
- Food Processing
- Workshop, DIY & MRO
Brand : Generic ( Made in India )
20 HP Rice Husk Grinding Machine
SKU : TI-2H-39737
MRP : ₹270000
₹213500
21% OFF!
-
1
+
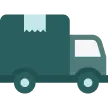
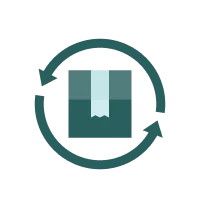
Easy Return
& Refund
& Refund
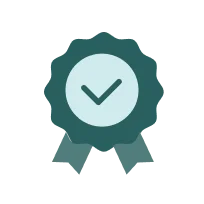
Quality
Assurance
Assurance
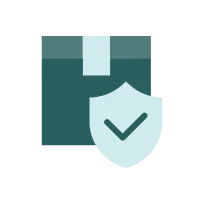
Trusted
Delivery
Delivery

After Sales
Assistance
Assistance
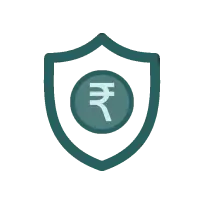
Buyer
Protection
Protection
Short Description
20 HP Rice Husk Grinding Machine
120-135 kg/hr Output Capacity
Country of origin: India
- Brand: Generic ( Made in India )
- Weight (Approx.) : 450 kg
- Material : Mild Steel
- Motor power - 20 HP
- Pulverizer machine size:
- First Chamber - 6" * 10"
- Second Chamber - 8" * 16"
- Production per hr - 120-135 kg/hr (depends on material)
- RPM- 2880
- Space Required - 6' * 6' * 8'
Note - The colour of the product may vary
This Rice Husk Grinding machine operates on an effective two-chamber pulverizing system, engineered for progressive size reduction of rice husks. A robust 20 HP motor drives the pulverizer at a high operational speed of 2880 RPM, ensuring efficient and consistent grinding. Rice husks are initially fed into the first chamber (6" x 10"), where primary grinding takes place, breaking down larger husk pieces. The partially processed material then moves into the larger second chamber (8" x 16") for finer pulverization. This sequential grinding process optimizes efficiency, allowing the machine to achieve a uniform and desired particle size for the final product. Constructed entirely from mild steel, the machine is built for longevity and offers good resistance to wear and tear, ensuring reliable performance over time. Its manageable weight of 450 kg provides stability during operation while making it relatively easier to transport and install compared to larger models.
Applications
:The 20 HP Rice Husk Grinding Machine, by converting raw rice husks into a fine powder, opens up a variety of valuable applications, especially for small to medium-scale operations. Here are the main applications of the product:
Biofuel and Energy Production:
- Briquettes and Pellets: The ground rice husk is an excellent raw material for producing biomass briquettes or pellets. These densified fuels are a clean, renewable alternative to fossil fuels for boilers, furnaces, and even domestic cooking. This machine's output capacity is suitable for local production of these fuels
- Direct Combustion: While less efficient in raw form, grinding allows for more uniform and complete combustion in specialized biomass burners, making it a viable fuel source for small industrial processes or even for drying paddy.
- Animal Feed Additives:
- Roughage/Filler: Ground rice husk, though low in nutritional value, can be used as a fiber-rich roughage or filler in animal feed formulations for livestock (e.g., cattle, poultry). It aids in digestion and adds bulk, especially when mixed with more nutritious ingredients.
Agriculture and Soil Amendments :
Compost Enhancement: Ground rice husks can be incorporated into composting piles as a carbon source, improving the aeration and structure of the compost.
Growing Medium: Due to their lightweight and good drainage properties, ground rice husks can be mixed into potting soils or used as a component in soilless growing mediums for nurseries and horticulture.
Construction Materials:Rice Husk Ash (RHA): When ground rice husks are subjected to controlled burning, the resulting ash (RHA) is rich in amorphous silica. This RHA is a highly reactive pozzolanic material.
Usage
:The usage of this 20 HP Rice Husk Grinding Machine centers on efficiently transforming raw rice husks into a finely powdered form. This process significantly increases the usability and value of rice husks, which are otherwise bulky agricultural waste.
- Material Input and Initial Grinding:
- Feeding: Raw rice husks, typically collected from rice mills, are fed into the machine's intake hopper. For this size of machine, feeding is often manual or via a simple screw conveyor.
First Chamber Processing: The husks first enter the 6" x 10" first chamber. Inside, high-speed rotating hammers or beaters impact and shatter the husks, performing an initial, coarser breakdown of the material.
2. Fine Grinding and Output Control:
Second Chamber Pulverization: The partially ground material then moves into the larger 8" x 16" second chamber. Here, the pulverization process is intensified, further reducing the particle size to the desired fineness.
Sizing and Discharge: A strategically placed screen at the outlet of the second chamber ensures that only particles meeting the required fineness pass through. Any oversized particles are retained within the chamber for continuous grinding until they reach the desired size. The finely ground rice husk powder is then discharged from the machine, typically collected into bags, bulk containers, or conveyed to the next stage of processing.
3. Core Function:
Volume Reduction & Property Enhancement:
The primary purpose of using this machine is to achieve:
Significant Volume Reduction: Raw rice husks are voluminous. Grinding them into powder drastically reduces their bulk, making storage, handling, and transportation much more economical and convenient.
Increased Surface Area: Pulverizing greatly increases the exposed surface area of the husks. This is crucial for their reactivity in subsequent applications like combustion, chemical reactions, or absorption, making processes more efficient.
Improved Uniformity & Flowability: Ground husks are far more uniform in particle size and flow much more smoothly than raw husks, which is essential for consistent feeding into other machinery (e.g., pellet presses, furnaces) or for mixing with other ingredients.
The finely ground rice husk powder produced by this 20 HP machine is then utilized as a valuable input material across various sectors:
For Energy Generation: The powder is used as a consistent feedstock for small-scale biomass boilers or gasifiers, or it's densified into briquettes or pellets for renewable fuel.
In Agriculture: It serves as a fiber-rich additive in animal feed or as a key ingredient for producing biochar to improve soil health and fertility. It's also used as a component in potting mixes and composting.
For Construction Materials: The ground husks are suitable for controlled burning to produce Rice Husk Ash (RHA), which can act as a pozzolanic additive in cement and concrete for smaller construction projects.
As Industrial Fillers/Absorbents: The finely ground material can be used as a base for activated carbon production or as an absorbent for spills, or even as a lightweight filler in various products.
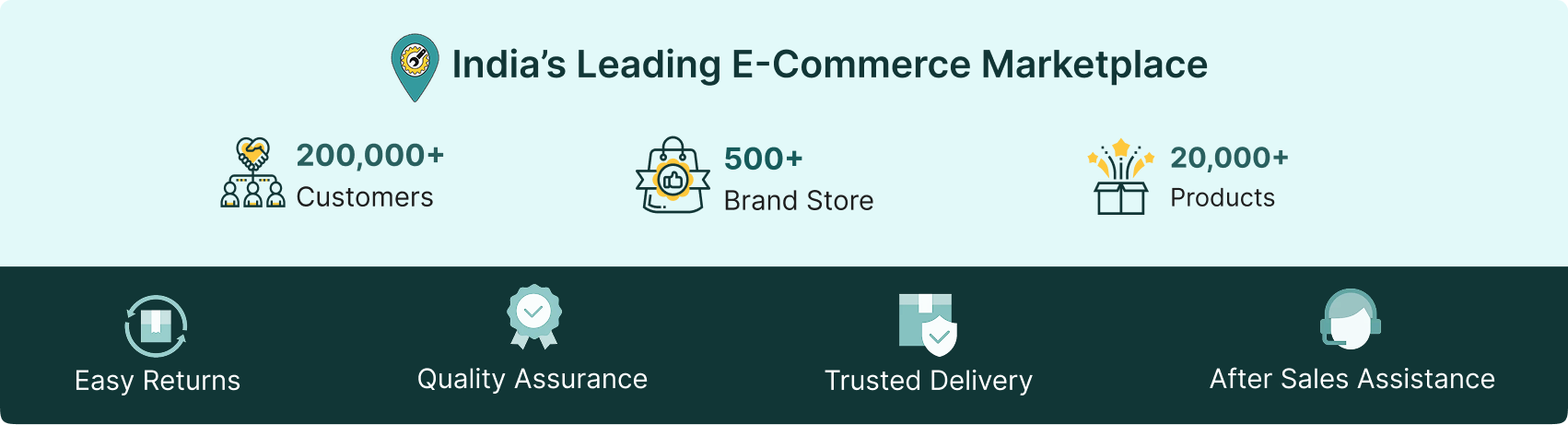

Select attribute
